Unmatched Commitment To Quality
Based on a more than 8D problem-solving model, Scot Forge’s corrective action system has given over a hundred employee-owners the opportunity to lead corrective action request teams. The company’s regularly scheduled Layered Process Audits involve all levels of leadership and provide key input to the effectiveness and sustainability of the quality system. With full company involvement and ownership, a commitment to quality is evident throughout Scot Forge.
Quality & Special Process Certifications
In July 1992, Scot Forge was the first North American open die forging company to be awarded certification to ISO 9001. Scot Forge has maintained certification since that time and currently has the certification to ISO 9001:2015 as well as AS9100D (EN 9100D:2016, JISQ 9100:2016). Ringmasters and North American Forgemasters, both joint ventures of Scot Forge, are also certified to ISO 9001:2015. Further pursuance of aerospace products has led to Nadcap accreditation in both Heat Treatment for aluminum material and Nondestructive Testing.
All products are produced under ISO 9001:2015 standards and can meet other accreditations including AS9100D, ABS, DNV, Lloyd's Register and the European Pressure Equipment Directive (PED) when specified by contract.
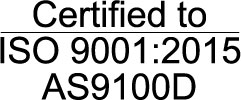
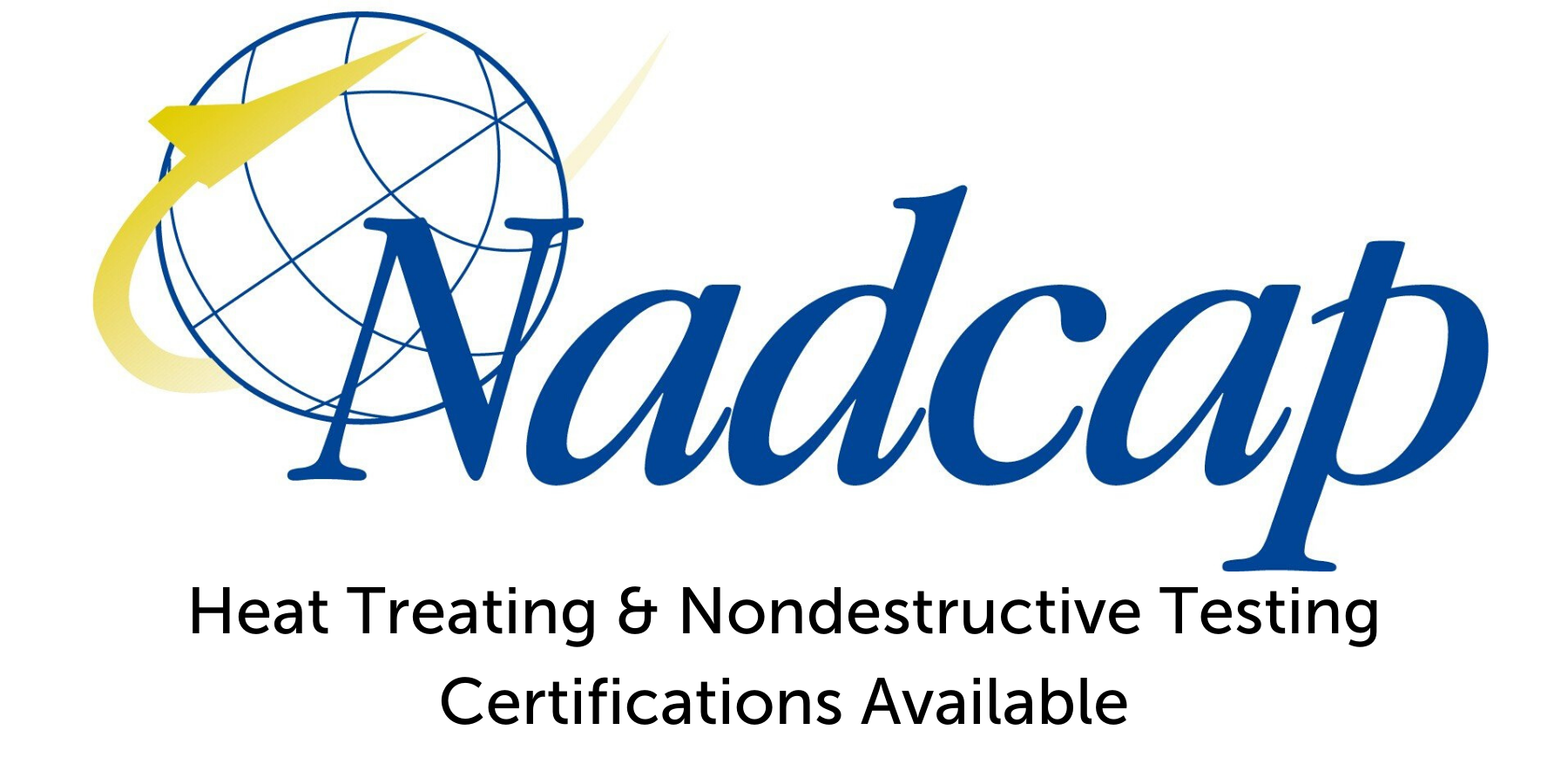